Why Is My Sewing Machine Needle Not Moving?
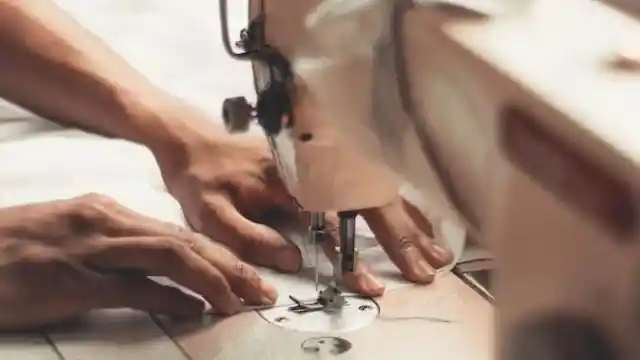
Sewing is a beloved hobby for many, but it can quickly become frustrating when your sewing machine needle won’t move. A stuck needle prevents you from completing your project and can even damage your machine if not addressed promptly.
In this comprehensive guide, we’ll explore the most common reasons a sewing machine needle may not be moving and provide solutions to get you sewing again.
Common Causes of a Stuck Needle
There are several potential causes of a stuck needle on a sewing machine. Here are some of the most common culprits:
Disengaged Clutch
Many sewing machines have a handwheel clutch that disengages the needle mechanism for bobbin winding. If this clutch remains disengaged, the needle won’t move when you start sewing.
Solution: Make sure the clutch is fully engaged before sewing. There is usually a screw or lever to tighten the clutch. Refer to your machine’s manual for details.
Broken Drive Belt
Another potential cause for the needle’s immobility could be related to issues with the sewing machine’s drive belt. The drive belt is responsible for connecting the motor to the gears, ensuring that the power generated by the motor is efficiently transferred to the needle. A worn or loose drive belt can disrupt this power transfer and prevent the needle from moving as intended.
Solution: Inspect the drive belt for signs of wear, tension, or damage, and consider replacing it if necessary.
Internal Drive Gear Failure
Another reason for the needle’s lack of movement could be attributed to a broken or worn-out gear within the sewing machine. Over time, the constant friction and stress from regular use can take a toll on the gears, causing them to deteriorate or even break. When a gear fails to function correctly, it disrupts the power transmission process, hindering the needle’s motion and causing it to jam in place.
Solution: This usually requires the expertise of a professional repair technician to fix.
Thread Caught in Shuttle Race
If thread gets jammed in the shuttle race (the area underneath the needle plate), it can prevent the needle from moving properly.
Solution: Remove the needle plate and carefully cut away any trapped threads around the shuttle race.
Upper Thread Tension Issue
If the thread tension is too tight, it adds friction that may halt the needle’s movement. Loose tension can have the same effect.
Solution: Adjust the tension according to your machine’s manual. Make small incremental turns to find the optimal tension.
Wrong Needle Size
Using the wrong needle size or type for your fabric and thread can cause needle jams and inhibit movement.
Solution: Refer to your machine’s manual to determine the right needle size. Consider the needle material as well.
Bobbin Case Dislodged
If the bobbin case underneath the needle plate gets knocked out of position, it can stop the needle from moving smoothly.
Solution: Remove the needle plate and reseat the bobbin case in the proper position. Secure any screws or spring locks.
Troubleshooting a Stuck Needle
If your sewing machine needle won’t move up and down, start troubleshooting with these steps:
1. Check Power and Machine Settings
- Make sure the machine is turned ON and plugged in.
- Check that all handwheels/clutches are tightened and engaged.
- Ensure the presser foot is lowered and sinker plate covers are installed.
- Reset any error codes or automatic needle stop functions.
2. Test Needle Movement Manually
- Rotate handwheel counterclockwise as far as it will go.
- Try to move the needle up/down by hand. If it won’t budge, continue troubleshooting.
3. Remove Trapped Threads
- Remove the needle plate and bobbin case.
- Cut away any threads trapped around the shuttle, feed dogs or handwheel.
- Clean out lint or debris with a brush.
4. Adjust Tension and Change Needle
- Check that thread tension is set correctly.
- Try a new needle in the recommended size for your project.
5. Inspect Internal Components
- Open up casing panels to expose belts, gears and motor.
- Look for broken, loose or jammed components like belts, gears or clutches.
- Consult a technician for repair if internal damage is found.
If the needle still won’t move after troubleshooting, it likely requires professional service to fix damaged parts. Contact the manufacturer or a sewing machine repair shop.
Frequently Asked Questions About Non-Moving Sewing Machine Needles
Here are answers to some frequently asked questions about sewing machine needle issues:
Why does my needle keep stopping mid-stitch?
Frequent needle stopping or hesitation usually indicates a timing issue where the needle and shuttle hook are misaligned. This causes the thread to catch or bind. Timing alignment needs professional adjustment.
What happens if I keep sewing with a stuck needle?
Forcing a jammed needle to keep sewing can damage the feed dogs, bending the needle, breaking threads and ruining fabric. Stop immediately if the needle won’t move and troubleshoot the cause.
Can hitting a pin while sewing cause needle issues?
Striking a pin or other object with the needle can bend it, throw off timing, break threads or damage internal gears. Stop and thoroughly inspect components if this occurs.
My needle won’t turn – does this require shop repairs?
It depends. Try lubricating, removing obstructions and testing components first. But issues like stripped gears, broken connections or motor failure will require professional service.
I replaced my needle and it’s still stuck – now what?
Other underlying problems are likely preventing needle movement. Keep troubleshooting tension, belts, clutches and internal gears. You may need a technician’s expertise.
Why does my needle keep breaking?
Frequent needle breaking often results from hitting pins, using dull or wrong sized needles, improper insertion or issues with hook timing that cause thread jams.
Does needle size really matter for sewing?
Absolutely! Needle size must be matched to the weight and type of fabric you are sewing. Using the wrong size can lead to skipped stitches, thread breaks, needle jams and poor stitch formation.
Preventing Future Needle Jams
Follow these tips to help prevent a stuck needle from happening again:
- Always unplug the machine before clearing jams, replacing needles or maintenance.
- Make sure needles are installed to the top of the shaft and secured tightly.
- Avoid hitting pins and pins by removing them before sewing. Use a pincushion.
- Use a new needle for each project and change it often. Bent, dull needles cause problems.
- Keep mechanisms clean and lint-free. Built-up lint can impede needle movement.
- Don’t pull fabric – let the feed dogs advance it to avoid needle deflection.
- Ensure timing is correctly calibrated. Off-kilter timing affects stitch formation.
- Always use the right size, point style and material needle for your fabric type.
- Check tensions frequently and re-thread top and bobbin threads before sewing.
- Consider having your machine professionally serviced yearly to fix minor hiccups before they become big problems.
When to Call a Sewing Machine Repair Technician
While many needle issues can be fixed at home, some situations call for a trained sewing machine repair technician:
- Internal damage such as stripped gears, broken bushings or faulty wiring.
- Bent or damaged components like needles, feed dogs or hook mechanisms.
- Removal of a needle stuck tight in the fabric or machine.
- Major timing misalignments causing extensive thread damage.
- Electrical issues with the foot pedal, power supply or internal circuits.
- Drive motors or belts that are malfunctioning or need replacement.
Technicians have specialized tools, testing equipment and expertise to efficiently diagnose problems and make precise adjustments and repairs. This can save time and money compared to struggling with a complex mechanical or electrical issue on your own.
Look for an experienced local sewing machine repair company with expertise servicing your machine make and model. Be sure to ask about service call fees, hourly rates and typical turnaround times.
When to Just Replace Your Sewing Machine
Older sewing machines with extensive mechanical wear may reach a point where repairs are no longer worthwhile. Signs that a machine may be beyond cost-effective repair include:
- No longer functions reliably even after multiple servicing attempts.
- Needed parts are discontinued or unavailable.
- Repair costs exceed 50% or more of a new machine price.
- Electrical components, motors and wiring are unsafe or obsolete.
- The machine frame is structurally damaged or majorly corroded.
- It cannot accurately sew modern fabrics and thread types.
Advances in sewing technology also make replacement compelling if your old machine lacks helpful features like easy needle threading, adjustable speed control and built-in stitch selection.
Upgrading to a new computerized machine can vastly expand your creative abilities. But you can also find reasonably-priced mechanical machines with modern convenience features. Compare repair costs to your budget and needs when deciding whether to mend or end your relationship with an aging sewing machine.
Conclusion
A seized needle can bring your sewing to a grinding halt, but don’t panic! In many cases, you can get your machine running smoothly again with a little investigation and DIY troubleshooting. Just be sure to pinpoint the cause and address it properly.
Knowing when to call in a trained repair technician can also save you money and frustration. With the right maintenance and care, your sewing machine should provide many years of trusty service and enjoyably stitching.